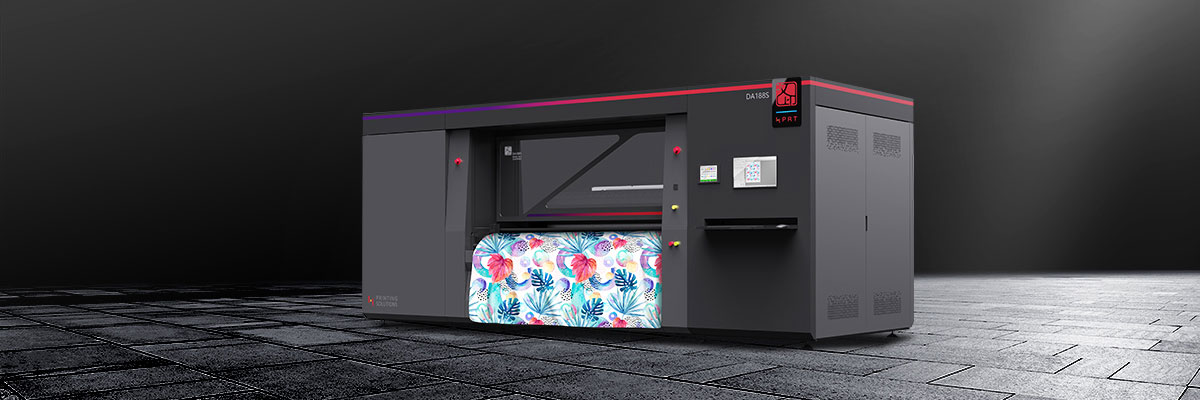
2. Plate-making and positioning techniques
Rotary Screen Printing
Platemaking:
Nickel screens are laser-engraved to create perforations matching the design. Each screen is calibrated for color and alignment, with mesh sizes varying from coarse (for solid colors) to ultra-fine (for gradients).
Positioning:
Screens are mounted on rotating cylinders, and magnets/squeegees inside ensure precise ink transfer. This method handles up to 16 colors and operates at speeds of 50–120 yards per minute, ideal for large batches.
Digital Precision Printing
Platemaking:
Nickel screens are laser-engraved to create perforations matching the design. Each screen is calibrated for color and alignment, with mesh sizes varying from coarse (for solid colors) to ultra-fine (for gradients).
Positioning:
Screens are mounted on rotating cylinders, and magnets/squeegees inside ensure precise ink transfer. This method handles up to 16 colors and operates at speeds of 50–120 yards per minute, ideal for large batches.
3. Inks and environmental innovation
Traditional Crafts:
Pigment-based inks dominate, with additives like binders and softeners tailored to fabric types (e.g., cotton vs. polyester).
Digital Breakthroughs:
2025 sees a surge in eco-friendly solutions, such as hydroxypropyl beta-cyclodextrin-enhanced inks (improving solubility and stability) and water-based dyes compliant with OEKO-TEX standards . Companies like Lanyu Co. are leading the charge, offering 3,000+ ink formulations for diverse applications.
4. Printing and post-processing
Printing:
Fabrics pass under screens or printheads, where ink is applied in layers. Digital printers use drop-on-demand technology to minimize waste, while traditional methods rely on continuous ink flow.
Color Fixing & Drying:
After printing, fabrics undergo steam curing (for dyes) or heat fixation (for pigments). Digital prints dry instantly via infrared heaters, reducing energy use by 30% compared to traditional ovens.
5. Quality control and customization
Printing:
Fabrics pass under screens or printheads, where ink is applied in layers. Digital printers use drop-on-demand technology to minimize waste, while traditional methods rely on continuous ink flow.
Color Fixing & Drying:
After printing, fabrics undergo steam curing (for dyes) or heat fixation (for pigments). Digital prints dry instantly via infrared heaters, reducing energy use by 30% compared to traditional ovens.
Industry Trends and Expert Opinions
The Rise of Digital Printing:
By 2025, 26% of global textile prints will be digital, driven by demand for fast-turnaround, eco-friendly production.
Sustainability:
The industry is shifting toward circular practices, including recycled inks and waterless processes. For example, Lanyu Co.’s new facility reduces water usage by 80%.
Technology Convergence:
Hybrid systems combining traditional and digital methods (e.g., rotary screens with AI alignment) are gaining traction for cost-effective, high-precision outputs.
Conclusion
Spring/Summer 2025 celebrates individuality through color, texture, and cultural storytelling. Whether opting for Uniqlo’s eco-friendly linen or Chanel’s dreamy pastels, this season invites everyone to embrace fashion that feels both personal and purposeful.
Key Takeaways:
Tradition meets modernity:
Rotary screen printing remains vital for large-scale production, while digital methods excel in customization and sustainability.
Environmentally friendly innovations:
Eco-friendly inks and energy-efficient processes are driving the industry toward a greener future.
Data-driven:
AI and real-time analytics are enhancing efficiency, reducing waste, and enabling hyper-personalization.
Post time: May-05-2025